انرژی یکی از بحثهای مهم و اصلی در تمام صنایع جهان است. میزان مصرف انرژی یکی از اصلیترین فاکتورهای تعیینکننده قیمت تمامشده محصولات محسوب میشود و سوی دیگر مصرف انرژی، خصوصا سوختهای فسیلی، آلودگیهای زیستمحیطی است. با توجه به اینکه صنعت فولاد جزو بزرگترین صنایع انرژیبر (خصوصا برق و گاز طبیعی) در میان صنایع مادر هر کشور به حساب میآید، بهینهسازی مصرف انرژی نقش بسزایی در مدیریت هزینههای تمامشده محصول و جلوگیری از انتشار گازهای گلخانهای و حفظ محیط زیست ایفا میکند.
بالا بودن کیفیت مواد اولیه (آهناسفنجی، قراضه و… )، روشهای بهینه کنترل فرایند، استفاده از تجهیزات با تکنولوژی بالا، کاهش توقفات اضطراری، استفاده از انرژی شیمیایی برای تامین بخشی از دمای کوره قوس الکتریکی در فرایند ذوب، بالا بودن کیفیت و ارزش حرارتی گاز طبیعی و نیز فرهنگسازی و آموزش منابع انسانی بهخصوص مشاغل مرتبط با تجهیزات بارز انرژی مهمترین عوامل تاثیرگذار بر کاهش مصرف انرژی در صنعت فولاد محسوب میشوند.
بر اساس آمارها، حدود یکسوم از کل برق مصرفی کشور متعلق به بخش صنعت است و حدود یکچهارم از این میزان در صنایع فولادی مصرف میشود که عدد قابلتوجهی به شمار میآید. با بهینهسازی مصرف انرژی در صنایع فولادی به میزان 10 درصد، میتوان یک درصد از کل برق مصرفی کشور را کاهش داد.
بهبود مصرف انرژی در فولاد هرمزگان
شرکت فولاد هرمزگان، در راستای مدیریت مصرف انرژی و کاهش هزینههای تولید، از سال 1393 کمیته انرژی را، متشکل از اعضای تصمیمگیرنده و مجرب، تشکیل داد. این کمیته خطمشی انرژی سازمان را تنظیم و تصویب کرد و بحث مدیریت مصرف انرژی در دستور کار قرار گرفت. در همین زمینه گواهینامههای مدیریت انرژی «2011-50001 ISO» در سال 1394 از شرکت «TUV intercert» و در سال 1396، به علت دستور یکسانسازی استانداردها، از شرکت «SGS» اخذ شده است. همچنین کمیته مدیریت انرژی شرکت فولاد هرمزگان، در راستای تحقق هدف استراتژیک «بهینهسازی مصارف عمده» و نیز بهبود عملکرد انرژی سازمان، در سال 1398 اقدام به ارتقای سیستم مدیریت انرژی موجود و اخذ استاندارد « 2018-50001 ISO» کرد. یکی از ویژگیهای مهم این استاندارد، یکپارچگی بهتر با فرایندهای مدیریت استراتژیک است. شرکت فولاد هرمزگان در بهمنماه 1398 موفق به اخذ این گواهینامه از شرکت «SGS» شده و در مهرماه 1399 ممیزی مراقبتی را با موفقیت به انجام رسانده است. استقرار این سیستم باعث ایجاد چارچوبی منظم و هدفمند برای بهینهسازی مصرف انرژی در راستای اهدف استراتژیک سازمان شده است.
واحدهای تولیدی حدود 99 درصد کل انرژی مجتمع را مصرف میکنند که عمده مصرف برق در واحد فولادسازی (حدود 80 درصد) است. حدود 96درصد گاز طبیعی نیز در واحد آهنسازی مصرف میشود. بنابراین تیم انرژی شرکت فولاد هرمزگان پتانسیلهای صرفهجویی در واحدهای تولیدی را شناسایی و پروژههای بهبود عملکرد انرژی را تعریف کرده است. یکی از اهداف اصلی این سازمان، تامین انرژی با مناسبترین قیمت است و مجتمع فولاد هرمزگان در این راستا، برای کاهش هزینه، بخشی از توان الکتریکی مورد نیاز خود به میزان 150 مگاوات را از شرکتهای خصوصی و بخشی از برق مورد نیاز را از طریق بورس انرژی خریداری کرده است. اقدام دیگر این مجتمع انتخاب گزینه مطلوب در قبوض برق با توجه به برنامه تولید محصول است. علاوه بر آن، مجتمع فولاد هرمزگان با شناسایی فرصتهای بهبود و انجام اقدامات و پروژههای موثر در چارچوب سیستم مدیریت انرژی، موفق به افزایش عملکرد انرژی سازمان به موازات افزایش میزان تولید محصول شده است. از جمله مهمترین پروژههای بهبود مصرف انرژی در شرکت فولاد هرمزگان در سالهای 1398 و 1399 میتوان به موارد زیر اشاره کرد:
- تثبیت انرژی الکتریکی کورههای قوس الکتریکی واحد فولادسازی؛
- جلوگیری از اتلاف انرژی حرارتی و الکتریکی در واحد آهنسازی با پروژه تعویض تیوپهای ریفورمر مدول A؛
- جلوگیری از اتلاف انرژی حرارتی و الکتریکی در واحد آهنسازی با پروژه بارگذاری کاتالیستهای جدید در مدول A؛
- کاهش مصرف انرژی الکتریکی واحد تولید گازهای صنعتی با پروژه نصب و راهاندازی کمپرسور اصلی «standby»؛
- کاهش مصرف انرژی حرارتی واحد آهکپزی با پروژه کاهش توقفات اضطراری و افزایش راندمان تولید؛
- کاهش مصرف انرژی الکتریکی کورههای قوس الکتریکی به میزان « kwh/ton heat 17»؛
- پروژه بهبود کیفیت سرباره؛
- پروژه کاهش نرخ مصارف گاز طبیعی و برق واحد احیای مستقیم به میزان «kwh/ton 5/0» و «Gj/ton 03/0»؛
- تثبیت مصرف گاز طبیعی در کوره آهکپزی در «Gj/ton Lime 04/3».
در نتیجه پروژههای بهبود انرژی در ده ماه نخست سال 1399 نسبت به سال 1398، این مجتمع موفق شد میزان مصرف برق کورههای قوس الکتریکی را به میزان «kwh/ton heat 15» کاهش دهد. همچنین مصرف برق واحد احیای مستقیم به میزان «kwh/ton dri 9/3» و مصرف گاز طبیعی این واحد به میزان«kwh/ton dri 17/0» کاهش یافته است. نمودار 1 بیانگر تلاش سازمان در اداره امور انرژی با بازدهی بالا و روند نزولی مصرف انرژی کل شرکت فولاد هرمزگان (Gj/tonslab) از سال 1394 تا سال 1398 است.
این شرکت به منظور مجهز شدن به مناسبترین تکنولوژی در زمینه مصرف انرژی در دو زمینه اقدام کرده است:
خرید تجهیزات با تکنولوژی بالا: در سیستم مدیریت انرژی، تجهیزات بارز انرژی (SEUs) شناسایی شده و مطابق گردشکار خرید، سازمان موظف به خرید تجهیزات با تکنولوژی بالا و کمترین میزان مصرف انرژی است. البته به خاطر مشکلات ناشی از تحریمهای اقتصادی، تحقق این امر با موانع زیادی همراه است.
طراحی (طرحهای اصلاح سیستمهای موجود و طرحهای توسعه): مطابق دستورالعمل اجرایی در واحد مهندسی کارخانه، در کلیه طرحهای اصلاحی و طرحهای توسعه شرکت، باید بهینه سازی مصرف انرژی مد نظر قرار گیرد. برای مثال، در طرح توسعه فولاد هرمزگان و افزایش ظرفیت تولید تختال تا 2 میلیون تن، از روش تزریق اکسیژن به صورت ساید وال (Side Wall Injection) استفاده میشود که اجرای این طرح باعث افزایش انرژی شیمیایی و به تبع آن کاهش مصرف انرژی الکتریکی در کورههای قوس الکتریکی خواهد شد.
در حال حاضر، در شرکت فولاد هرمزگان، به منظور مدیریت مصرف و هزینه انرژی، اقدامات گستردهای شده است شامل بهینهسازی زمانهای توقف، انجام توقفات برنامهریزیشده در زمانهای اوج بار (پیک قیمت برق) و همچنین کاهش توقفات اضطراری که باعث پیوستگی تولید و در نتیجه، افزایش میزان تولید و کاهش تلفات انرژی میشود.
گفتنی است که یکی از رویکردهای اساسی شرکت فولاد هرمزگان کاهش انتشار گازهای گلخانهای است. این مجموعه، با اجرای درست سیستم مدیریت انرژی و نیز ترکیب این سیستم با سیستمهای دیگر نظیر استاندارد محیط زیست، به دنبال کاهش انتشار گازهای گلخانهای و دستیابی به اهداف کاهش تغییرات اقلیمی است. در این راستا، این مجموعه در سال 1398 اقدام به اخذ گواهینامه محیط زیست کرد و در مهرماه سال جاری موفق به کسب استاندارد «2015-14001 ISO» محیط زیست از شرکت «SGS» شد.
رويکردی برای کاهش مصرف آب
آب صنعتی مورد نیاز واحدهای فولاد هرمزگان توسط دو دستگاه پمپ عمودی سانتریفیوژ، با ظرفیت هرکدام 3 هزار و 350 متر مکعب بر ساعت، از دریا برداشت و توسط دو خط انتقال «GRV» به قطر نهصد میلیمتر و طول یک هزار و 500 متر از اسکله به واحد آبشیرینکن در سایت جنوبی شرکت ارسال میشود. در واحد آبشیرینکن، پس از انجام عملیات پیشتصفیه شامل کلرزنی، آشغالگیری، کلاریفایر و فیلترهای شنی، آب با عبور از فیلترهای کارتریج پنج میکرون، وارد مرحله تصفیه به روش اسمز معکوس میشود. ظرفیت تولید آب صنعتی توسط این واحد 25هزار و 200 متر مکعب در روز و میزان «TDS» و کلراید آب صنعتی تولیدی بهترتیب «mg/lit 390» و «mg/lit 230» است. آب صنعتی تولیدی توسط دو دستگاه پمپ سانتریفیوژ و خط انتقال دفنی «GRP» به قطر هفتصد میلیمتر و طول 3 هزار و 800 متر به سایت شمالی مجتمع (واحد توزیع سیالات) انتقال مییابد.
سیستم پیشتصفیه آبشیرینکن، به علت مشکلات طراحی، دارای راندمان مطلوب نبوده، اما با ایجاد تغییر در سیستم فیلتراسیون، عملکرد کمّی و کیفی این سیستم تا حدودی ارتقا یافته است. در حال حاضر، به منظور افزایش تولید این واحد تا تولید نامی (m3/h 1050)، پروژه اصلاح این سیستم، تعریف شده و در حال اجرایی شدن است.
مدیریت در مصرف آب یکی از اهداف استراتژیک شرکت فولاد هرمزگان محسوب میشود. در این راستا، با انجام اقداماتی نظیر کاهش مقدار هدررفت و دورریز آب در واحدهای بهرهبرداری از طریق انجام منظم تعمیرات برنامهریزیشده بر روی برجهای خنککن، تجهیزات و خطوط توزیع آب، بهبود کیفیت آب تولیدی و استفاده از پساب فاضلاب بهداشتی به منظور آبیاری فضای سبز، مصرف آب مجتمع روند کاهشی داشته است. نمودار 2 روند کاهشی مصرف آب در شرکت فولاد هرمزگان بر حسب «/m3» را نشان میدهد.
در حال حاضر، پروژه بازچرخانی آب از طریق پروژه ساخت تصفیهخانه پسابهای سطحی در واحد آهنسازی به منظور بهینهسازی در مصرف آب مجتمع تعریف شده و در حال اجراست.
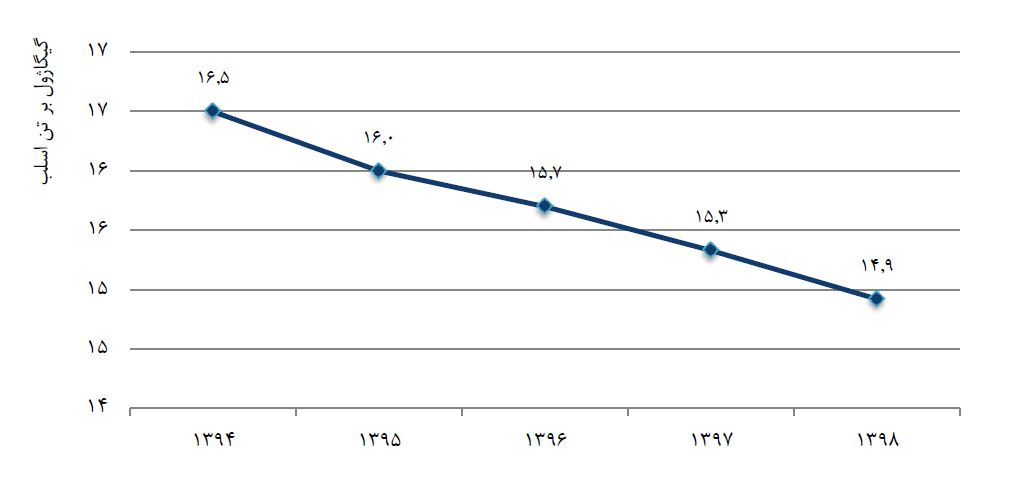
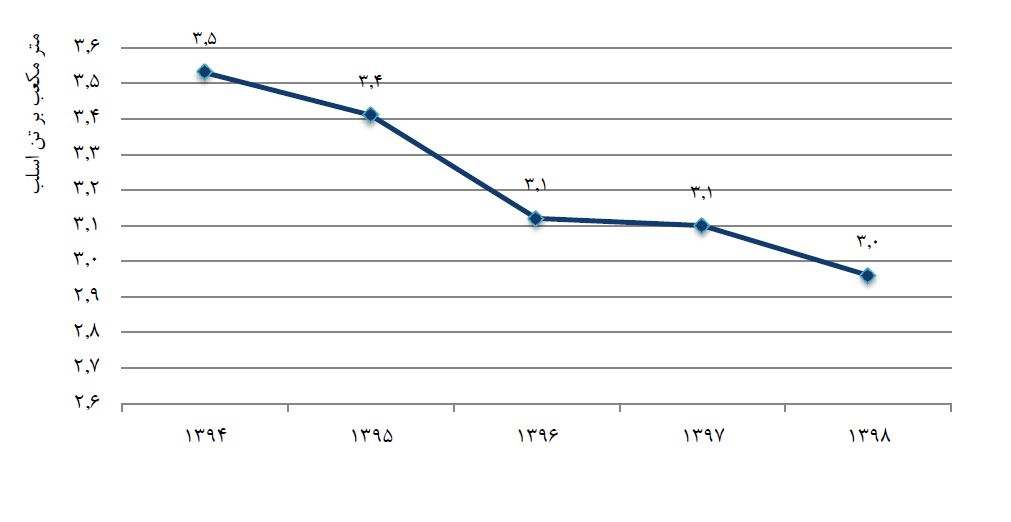
انتهای پیام/
ثبت دیدگاه