در سالهای اخیر، نوسانات اقتصادی کشور شرایطی ناپایدار را برای فعالیت بنگاههای اقتصادی ایجاد کرده است. کنترل نرخ رشد بهای تمامشده در شرایط تورمی موجب افزایش سودآوری و در نتیجه، ایجاد فرصتهای بهینهتر برای سرمایهگذاری و تسریع در اجرای پروژههای افزایش ظرفیت و نوسازی میشود که این مسئله خود موتور محرک کاهش بهای تمامشده در آینده خواهد شد. مدیریت بهای تمامشده، ضمن افزایش سودآوری، منجر به تاثیر مستقیم در بهینهسازی ساختار نقدینگی و تابآوری سازمان در شرایط رقابتی میشود. نفوذ در بازارهای جدید مصرف مستلزم سرمایهگذاری در کیفیت محصولات و قیمتهای رقابتی با سایر عرضهکنندگان است و این امر محقق نمیشود، مگر با مدیریت هزینههای تولید و بهای تمامشده محصولات. صنعت فولاد نیز، که امروز بخش بزرگی از اقتصاد و صادرات کشور را به خود اختصاص میدهد، از این قاعده مستثنا نیست و لازمه اساسی تداوم حضور و نقشآفرینی این صنعت در بازارهای جهانی، اجرای اقدامات مناسب در مسیر ارتقای بهرهوری، کاهش هزینههای تولید و مدیریت و کنترل بهای تمامشده محصولات است.
مواد اولیه و انرژی، چالشهای آینده صنعت فولاد
در فرایند تولید فولاد عواملی متعدد بر بازدهی و بهرهوری خطوط تولید و بهای تمامشده محصولات اثرگذار هستند. به همین دلیل، میتوان گفت که کاهش بهای تمامشده محصولات مستلزم تعیین یک استراتژی جامع و فراگیر در راستای ارتقای بهرهوری همه بخشهای خطوط تولید است. در همین راستا لازم است تا شرکت فولاد خوزستان نیز از چندین جنبه پارامترهای موثر بر قیمت تمامشده محصولات خود را کنترل کند.
نخست، با توجه به اینکه سهم انرژی (برق و گاز) در فرایند تولید و نیز تاثیر آن بر بهای تمامشده قابل توجه است، در بهبود و نوسازی تجهیزات به منظور کاهش نرخ مصرف، باید پایشهایی همیشگی صورت گیرد. همچنین، از آنجا که شرکت فولاد خوزستان در جنوب غربی ایران واقع شده است و نیز به سبب دوری آن از معادن سنگآهن کشور، نسبت به سایر فولادسازان هزینه بیشتری را برای حمل مواد اولیه (به صورت جادهای و ریلی) متحمل میشود. با هدف حل کردن این مشکل، این شرکت توانسته است که با استفاده از ترکیب حمل، هزینههای حمل خود را تا حد قابل ملاحظهای مدیریت کند. همچنین فولاد خوزستان، با استفاده از مواد اولیه باکیفیت، توانسته است هزینه ضایعات را به نحوی مدیریت کند که با تولید بیشتر، هزینههای ثابت به ازای هر تن را کاهش دهد و به این ترتیب، قیمت تمامشده تولید را متعادل کند.
با توجه به افزایش تولیدکنندگان فولادی و محدودیت منابع معدنی داخلی و محدودیتهای واردات و عرضه سنگآهن در بازار بورس و لغو محدودیتهای صادرات سنگآهن در سالهای آینده، بازار رقابتیتری برای تهیه مواد اولیه صنعت فولاد شکل خواهد گرفت و بر همین اساس، میتوان پیشبینی کرد سهم مواد اولیه مصرفی در قیمت تمامشده فولاد روندی افزایشی را طی کند.
شرکت فولاد خوزستان، با توجه به سهم بالای مواد اولیه در بهای تمامشده صنعت فولاد و نیز چشمانداز رشد آن، رویکردهای مختلفی را در این خصوص در دستور کار قرار داده است. سرمایهگذاری در شرکتهای تولید کنسانتره سنگآهن در سطح کشور به منظور تخصیص و برخورداری از سهم مناسب از تولید آنها یکی از رویکردهای اصلی این شرکت به شمار میآید که موجب تسهیل دسترسی و کاهش هزینههای تامین مواد اولیه خواهد شد. این شرکت همچنین در همین راستا سرمایهگذاری در افزایش ظرفیت تولید گندله سنگآهن و بهینهسازی و نوسازی واحدهای موجود را در دستور کار قرار داده است. بدیهی است که تامین پایدار مواد اولیه صنعت فولاد عامل مهمی در ارتقای آمار تولید به ظرفیت اسمی محسوب میشود که این مسئله خود سبب کاهش بهای تمامشده محصولات خواهد شد.
شرکت فولاد خوزستان همچنین افزایش ظرفیت واحدهای آهنسازی را در دستور کار خود قرار داده است تا به این ترتیب، با جایگزینی تولید آهن اسفنجی به جای خریداری آن، گام مهمی را در ایجاد ارزش افزوده و کاهش هزینههای تولید و بهای تمامشده محصولات خود بردارد.
یکی از چالشهایی که بهخصوص در ماههای اخیر تولید صنعت فولاد و بهای تمامشده این صنعت را بهشدت تحت تاثیر قرار داده قطعیهای برق بوده است. در همین راستا شرکت فولاد خوزستان تلاش دارد تا با سرمایهگذاری در تولید پایدار انرژی الکتریکی در قالب پروژه نیروگاهی و خرید سهام شرکتهای نیروگاهی برق و ایجاد پست توزیع، در مسیر به حداقل رساندن محدودیتهای استفاده از برق در شبکه سراسری و کاهش تولید ازدسترفته حرکت کند.
رویکردهایی برای مدیریت بهای تمامشده
مدیریت بهای تمامشده محصولات برای شرکتی مانند فولاد خوزستان، که بزرگترین عرضهکننده شمش فولاد کشور است و در مسیر توسعه صادرات حرکت میکند، بسیار اهمیت دارد. استراتژی اصلی فولاد خوزستان در زمینه مدیریت بهای تمامشده، سرمایهگذاری در بالادست و پاییندست زنجیره فولاد و کنترل نسبی عوامل تاثیرگذار بر قیمت تمامشده اقلام مواد اولیه از جمله کاهش هزینههای حمل با استفاده از حمل ترکیبی مواد است. خرید و انبارش مواد در فصول کاهش تقاضای بازار مواد اولیه و استفاده از توافقات بلندمدت یکی دیگر از راهکارهای خرید اقتصادی و کاهش ریسک در این خصوص محسوب میشود.
شرکت فولاد خوزستان در زمینه انرژی نیز طرح جایگزینی تولید انرژی پایدار با بخشی از خرید انرژی از بورس انرژی و همچنین ابتیاع سهام نیروگاههای برق را در دستور کار قرار داده است. طرحهای بهینهسازی مصرف برق و گاز در واحدهای تولید تعریف شدهاند و در برنامهای زمانبندیشده، سرمایهگذاریهای مناسبی به منظور نوسازی تجهیزات اثرگذار در نرخ مصرف انرژی در حال انجام شدناند.
شرکت فولاد خوزستان، با توجه به قدمت و تجربه کارکنان در زمینه تولید و تعمیرات، توانسته است در زمینه کاهش هزینههای قطعات و تعمیرات، کاهش ضایعات تولیدی و نیز کاهش نُرم مصارف مواد و انرژی و نسوز گامهایی بردارد و به عنوان یک مرجع، تجربههای خود را به سایر شرکتهای تولیدی منتقل کند.
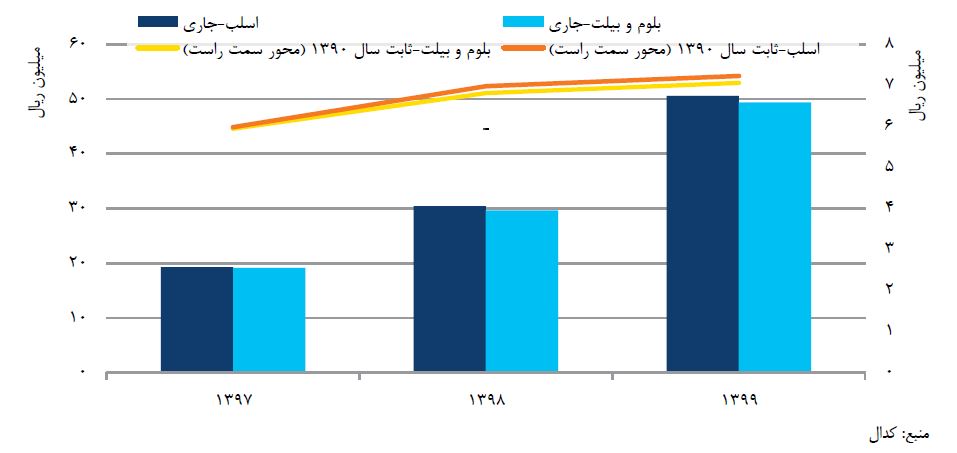
انتهای پیام/
ثبت دیدگاه