آلومینیوم یکی از صنایع استراتژیک و پرمصرف در بخش انرژی محسوب میشود. انرژی مصرفی سهمی بین 30 تا 40 درصد از هزینه تولید آلومینیوم را دارد؛ از این رو، مدیریت مصرف انرژی میتواند مقدار قابلملاحظهای از هزینه نهایی تولید را کاهش دهد. در سالهای اخیر و در میان تمامی صنایع پرمصرف، صنعت آلومینیوم بیشترین میزان رشد را در نرخ مصرف انرژی داشته است، به طوری که انتظار میرود تا سال 2040 میلادی این مصرف دوبرابر شود.
از آنجایی که هیچگاه نمیتوان انرژی را از محیط زیست تفکیک کرد، تمامی موسسات انرژی در کشورهای مختلف همواره این دو مبحث مهم را با هم بررسی میکنند. بهینهسازی تکنولوژیهای موجود و یا تعویض تکنولوژی با فناوریهای بهروزتر، در حالت کلی، میتواند کمک شایانی کند به کاهش مصرف مواد اولیه و انرژی، کاهش نیروی انسانی، افزایش عمر تجهیزات و در نتیجه کاهش مصرف لوازم یدکی، افزایش ضریب ایمنی و بهداشت کارکنان و کاهش ضایعات و در نتیجه کاهش آلودگی محیط زیست، به طوری که با بهکارگیری فناوریهای جدید در صنعت آلومینیوم، میتوان از 5 تا 30 درصد در مصرف انرژی صرفهجویی کرد. همچنین، با بهینهسازی فناوریهای موجود مخصوصا در بخش ذوبکننده، میتوان شدت انتشار «CO2» در محیط زیست را به میزان دو تن به ازای هر تن آلومینیوم تولیدی کاهش داد. از مهمترین ویژگیهای زیستمحیطی تکنولوژیهای جدید صنعت آلومینیوم میتوان به افزایش پالایش آلودگیها در حین تعویض آند سلولهای احیا، سیستم بسته انتقال آلومینا و کک و کنترل آلایندهها و گردوغبار ایجادشده در سیستم با راندمان بالا اشاره کرد.
صنعت آلومينيوم، صنعتی پرمصرف
سهم صنعت آلومینیوم از مجموع مصرف انرژی در کل صنعت کمتر از 5 درصد است. مصرف الکتریسیته در تولید آلومینیوم اولیه بهشدت بالاست که این امر یکی از دلایل اصلی بالا رفتن قیمت محصول نهایی است. بنابراین، با وجود کوچک بودن نسبی این صنعت، میانگین مصرف جهانی برق در صنعت آلومینیوم بسیار قابلتوجه است که این نکته اهمیت مدیریت مصرف انرژی و به تبع آن کاهش هزینه انرژی را آشکار میسازد؛ مسئلهای که میتواند قیمت تمامشده محصول تولیدی را به میزان قابلملاحظهای کاهش دهد و بر میزان رقابتپذیری آن بیفزاید. پرمصرفترین بخشهای صنعت آلومینیوم شامل پالایش آلومینا (آلومینیوم اکسید) است که در آن آلومینا از بوکسیت تولید میشود و نیز احیای آلومینیوم که در آن آلومینا به آلومینیوم تبدیل میشود. مرحله احیای آلومینیوم بیشترین مصرف انرژی الکتریکی را دارد و تقریباً 50 درصد انرژی در این فرایند تبدیل به گرما میشود. تولید آندهای کربنی با بازدهی کامل نیز تقریبا چهارده گیگاژول انرژی به ازای هر تن آلومینیوم تولیدی به این میزان انرژی اضافه خواهد کرد. جدول 1 انرژی مصرفی بخشهای مختلف به ازای تولید هر تن شمش آلومینیوم را نشان میدهد.
طبق گزارش بازدهی انرژی برای صنعت آلومینیوم اتحادیه اروپا در سال 2015، مراحل تولید شمش آلومینیوم در مجموع نزدیک به 58 گیگاژول انرژی الکتریکی برای هر تن آلومینیوم تولیدی مصرف میکند. تولید آلومینیوم از ضایعات (جدید و قدیم) نزدیک به 3.8 گیگاژول انرژی گرمایی و 0.45 گیگاژول انرژی الکتریکی به ازای هر تن آلومینیوم تولیدی استفاده میکند.
از عمدهترين پيشرفتهای فنی و تكنولوژيكی در صنعت توليد آلومينيوم، افزايش جريان برق (آمپراژ) و به تبع آن افزايش بازدهی توليدی آلومینیوم (راندمان) در واحد زمان و كاهش مصرف انرژی و برخی مواد مصرفی عمده نظير آند و آلومينيوم فلورايد به ازای توليد هر كيلوگرم آلومينيوم است. اهميت افزايش آمپراژ به حدی است كه عملا معيار اندازهگيری برای ميزان پيشرفتگی و مدرن بودن فناوریهای مختلف در اين صنعت محسوب میشود. در سالهای اخير، ديگهای احيا با شدت جريان دویست تا ششصد كيلوآمپر و با سيستم آندهای پيشساخته (پخته) مورد توجه فراوان در كشورهای مختلف جهان قرار گرفته است. شایان ذکر است که هماکنون تکنولوژیهای با آمپراژ بالاتر نیز در دست توسعه قرار دارند.
در سیاستگذاریهای جدید، شدت انرژی در صنعت آلومینیوم هرساله (2013 تا 2040) یک درصد کاهش پیدا کرده است که 60 درصد از این کاهش شدت انرژی به دلیل افزایش استفاده از فلزهای ضایعاتی است. از آنجایی که هزینههای بالای سرمایهگذاری چالشی مهم محسوب میشود، بهترین روشهای بازدهی مصرف الکتریسیته در این صنعت شامل بهبود فرایندهای ذوبکاری و تغییر مسیر آرام به سمت تکنولوژیهای کارآمد برای ذوبکاری آلومینیوم خواهد بود. شدت انرژی این صنعت میتواند با دو روش افزایش بازدهی انرژی و افزایش استفاده از ضایعات آلومینیوم کاهش پیدا کند. تولید آلومینیوم از ضایعات آلومینیوم تنها حدود 10 درصد از انرژی مصرفی در تولید آلومینیوم اولیه را احتیاج دارد.
تکنولوژی، عاملی برای کاهش مصرف انرژی
با توجه به مصرف بسیار بالای توان راکتیو در صنایع تولید آلومینیوم، شرکت آلومینیوم المهدی در راستای کاهش مصرف انرژی و اصلاح ضریب توان، اقدام به نصب و راهاندازی سیستم جبرانساز توان راکتیو با ظرفیت 140 مگاوار کرده است. این اقدام، کمک موثری به آزادسازی ظرفیت نیروگاه بندرعباس و شبکه برق منطقهای و کشوری، کاهش مصرف سوختهای فسیلی و کاهش آلودگی هوا کرده است. همچنانکه در نمودار 1 میتوان دید، با ورود پلههای سیستم جبرانساز به مدار، ضمن آزاد شدن ظرفیت نیروگاه بندرعباس پروفیل ولتاژ باسهای منطقه به میزان قابلملاحظهای بهبود مییابد.
با توجه به نوع تکنولوژی مورد استفاده در واحدهای تولید آلومینیوم کشورهای حاشیه خلیج فارس، نحوه عملکرد آنها و رقابت عمدهشان در کاهش مصرف انرژی برای تولید هر کیلوگرم آلومینیوم بسیار حائز اهمیت است. بیشترین میزان مصرف انرژی مربوط به واحدهای قدیمیتر و کمترین آن مربوط به واحدهای با تکنولوژیهای جدید و پیشرفته است. با نگاهی به ظرفیتهای مشخصشده از هر واحد تولیدی و دادههای آماری، میتوان اذعان داشت که برخورداری واحدهای تاسیسشده از تکنولوژیهای بهروزتر، بیشترین تاثیر را در کاهش میانگین مصرف انرژی برای تولید هر واحد آلومینیوم در منطقه داشتهاست.
با پیشرفت تکنولوژی، قطعا استانداردهای سختگیرانهتری نیز برای مصرف انرژی بهویژه در تمامی صنایع، بهخصوص صنعت آلومینیوم، در نظر گرفته خواهد شد. همانطور که ایران برای کارخانههای جدیدالاحداث عدد پانزده کیلووات ساعت بر کیلوگرم را در نظر گرفته است، اروپا نیز در سال 2018 عددی بهمراتب کمتر از 1/16 را در نظر خواهد گرفت.
از آنجایی که الکتریسیته بیش از 90 درصد انرژی مصرفی در فرایند تولید آلومینیوم اولیه را در اختیار دارد، تمامی تحقیقات بر بهینهسازی این بخش از فرایند تولید متمرکز شدهاند. بنابراین، با بررسی و شناخت مصرف الکتریسیته در فرایند تولید آلومینیوم در مناطق مختلف جهان، میتوان مسیر بهتر و درستتری را برای بهینهسازی مصرف الکتریسیته در فرایند تولید آلومینیوم در کشور انتخاب کرد. افزايش جريان برق (آمپراژ)، به عنوان یکی از عمدهترين پيشرفتهای فنی و تكنولوژيكی در صنعت توليد آلومينيوم، افزايش بازدهی توليدی آلومینیوم (راندمان) در واحد زمان و كاهش مصرف انرژی را به همراه خواهد داشت. هدفگذاری شرکت آلومینیوم المهدی در راستای ارتقای تکنولوژی تولید آلومینیوم به سطح 450 کیلوآمپر، با هدف تولید بیشتر با میزان انرژی مصرفی کمتر، شایانتوجه است. این شرکت اقدامات اولیه در راستای استقرار سیستم مدیریت انرژی (50001 ISO) را انجام داده و پیگیر استقرار کامل این سیستم است. همانگونه که گفته شد، شرکت آلومینیوم المهدی موفق به اخذ گواهی انطباق معیار مصرف انرژی در صنعت تولید شمش آلومینیوم برای مدیریت و کاهش مصرف انرژی شده است.
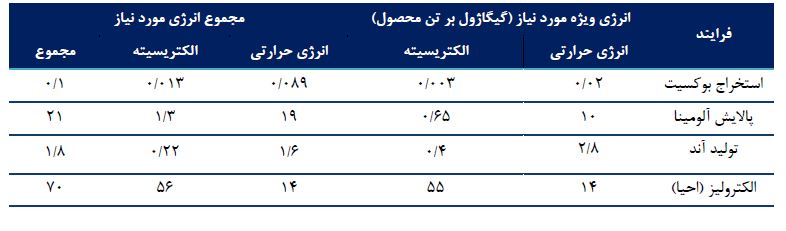
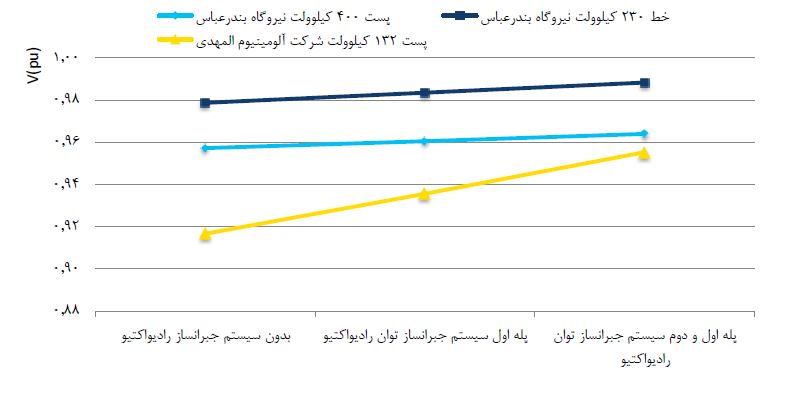
انتهای پیام/
ثبت دیدگاه