سودآوری نشاندهنده ظرفیت سود کسبشده برای شرکت با استفاده از وجوه یا سرمایه موجود، در نتیجه فعالیتهای انجامشده در یک دوره زمانی است. صنعت فولاد، با توجه به ظرفیتهای فراوان طبیعی و معدنی کشور، یکی از مهمترین صنایع اثرگذار در رشد اقتصادی کشور به شمار میآید. حملونقل هوایی، صنعت خودروسازی، ساختوساز و سایر بخشهای تجاری، همگی به مصرف فولاد متکی هستند که این امر فرصت مناسبی را برای توسعه بازارهای صادراتی محصولات فولادی ایجاد میکند. شرکتهای فولادی برای فروش حداکثری محصولات خود نیاز به تولید محصولی با بالاترین کیفیت و کمترین هزینه دارند. کاهش بهای تمامشده محصولات فولادی یکی از اصلیترین چالشها و اهداف واحدهای تولید محصولات فولادی به شمار میآید که این شرکتها را قادر میسازد تا با کاهش قیمت محصولات در مقایسه با سایر رقبای خود، سهم بیشتری از بازار را از آن خود کنند و فروش و سودآوری خود را افزایش دهند. به بیان دیگر، واحدهای فولادی برای ادامه بقا در بازارها، باید بهترین قیمت را برای محصولات و خدمات خود ارائه دهند و دستیابی به این مهم تنها در صورتی امکانپذیر است که با برنامهریزی مستمر و مناسب، بهای تمامشده محصولات خود را تا حد امکان مدیریت کنند و کاهش دهند.
در سالهای اخیر، نوسانات ارزی و افزایش هزینههای مواد اولیه تاثیراتی قابلتوجه بر پایداری و رشد صنعت فولاد کشور داشتهاند. برای جبران فشارهای داخلی و خارجی و کنترل مشکلات فعلی، لازم است تا شرکتهای فولادی بر اجرای سیاستهای مختلف به منظور کاهش هزینههای عملیاتی و بهبود کیفیت محصولات تمرکز کنند.
بهای محصول فولادسازان
سنگآهن ماده اصلی مورد نیاز برای تولید فولاد است. توسعه واحدهای فعال در عرصه فولاد کشور تقاضا برای این ماده معدنی را افزایش داده است. این در حالی است که ذخایر و تولید سنگآهن در کشور محدودیتهایی دارد. به نظر میرسد که در آینده، بازار سنگآهن شرایطی ناپایدار و نامشخص خواهد داشت. بدیهی است که افزایش قیمت سنگآهن در کشور موجب بالا رفتن بهای تمامشده محصولات فولادی میشود که این مسئله به میزان چشمگیری بر حضور ایران در بازارهای بینالمللی اثرگذار خواهد بود. از طرف دیگر، افزایش قیمت فولاد، به عنوان ماده اولیه بسیاری از صنایع کشور، موج تورمی بزرگی را به دنبال خواهد داشت و موجب تضعیف اقتصاد کشور خواهد شد. از این رو، به منظور جلوگیری از این پیامدها، لازم است تا برنامهریزی مناسبی در زمینه اکتشاف ذخایر سنگآهن و افزایش تولید این ماده معدنی انجام شود.
در سالهای اخیر، افزایش ناخالصیهایی نظیر سیلیس، گوگرد و فسفر در کنسانتره و گندله تولیدی در کشور موجب کاهش کیفیت و خلوص سنگآهن شده است. وجود این مواد، در کنار کاهش کیفیت تولیدات، موجب افزایش هزینهها برای ساخت محصولات فولادی میشود. در حوزه صنعت فولاد، حذف اینگونه عناصر به دلیل صرف انرژی بسیار بالا برای ذوب، هزینههای زیادی را بر شرکتهای فولادی تحمیل میکند. از این رو، حذف اینگونه مواد در مراحل اولیه تولید مواد معدنی، تاثیر بسزایی در کاهش بهای تمامشده محصولات فولادی دارد. شایان ذکر است که برای حذف مواد زاید در مراحل اولیه زنجیره فولاد نیاز به صرف هزینه بالا نیست. علاوه بر این، از آنجایی که صنایع فولادی نیازمند صرف انرژی بالا و حرارت هستند، مدیریت بهرهوری انرژی و منابع طبیعی کمک بسزایی در کاهش هزینهها و در پی آن بهای تمامشده محصولات فولادی میکند.
عوامل گوناگونی همچون بهرهوری نیروی انسانی، ماشینآلات، تجهیزات و منابع مالی از جمله پارامترهایی هستند که میتوانند بر قیمت تمامشده محصولات فولادی در کشور تاثیر بگذارند. اتخاذ سیاستهای مناسب و شناسایی عوامل موثر در کاهش یا افزایش بهرهوری، هزینههای خرید مواد اولیه و هزینههای سربار میتواند زمینهساز کاهش بهای تمامشده محصولات تولیدی شود. تهیه و استفاده از ماشینآلات مجهز به فناوری و تکنولوژیهای نوین بسیار هزینهبر است؛ از این رو، شرکتهای تولیدی تجهیزات و ماشینآلات مصرفی در صنعت فولادسازی، با بومیسازی تکنولوژیها، میتوانند گام موثری در کاهش هزینهها بردارند. همچنین در شرایط فعلی بیثبات بازار فولاد، فراهم آوردن زیرساختهای مناسب حملونقلی و کاهش هزینههای حملونقل مواد اولیه و محصولات نیز میتواند به کاهش هزینههای سربار و در انتها کاهش بهایتمامشده محصولات فولادی کمک کند.
کاهش بهای تمامشده، چالش صنعت فولاد
در حال حاضر و با توجه به شرایط موجود در کشور، مدیریت هزینه تمامشده به یکی از چالشهای اساسی در صنعت فولاد بدل شده است. از این رو، شرکت مجتمع جهان فولاد سیرجان همواره تلاش داشته است تا با اتخاذ سیاستهایی جامع، در مسیر مدیریت و کاهش هزینههای تولید خود گام بردارد. احداث طرحهای توسعه و افزایش ظرفیت تولید یکی از عوامل تاثیرگذار در رشد درآمدها، سودآوری و نیز کاهش بهای تمامشده محصولات فولادی است. این شرکت به منظور تولید محصولات نهایی و افزایش ظرفیت تولیدات خود، اقداماتی نظیر راهاندازی طرحهای توسعه همچون کارخانه ذوب و ریختهگری شماره 1 با ظرفیت یک میلیون تن در سال، اجرای پروژه خط کلاف نورد بردسیر با ظرفیت تولید 300 هزار تن در سال و اجرای پروژه فولادسازی شماره 2 با ظرفیت تولید 1.3 میلیون تن در سال را در دستور کار خود قرار داده و توانسته است نقشی کلیدی در تکمیل زنجیره تامین فولاد منطقه سیرجان ایفا کند.
درآمدهای عملیاتی این مجموعه، با رشدی 5.5 برابری نسبت به سال 1394، به رقمی حدود 22 هزار میلیارد ریال رسیده است. در نمودار 1، نسبت بهای تمامشده به درآمد عملیاتی شرکت مجتمع جهان فولاد سیرجان نشان داده شده است. چنانکه دیده میشود، نسبت بهای تمامشده به درآمدهای عملیاتی شرکت مجتمع جهان فولاد سیرجان در سالهای اخیر روندی نزولی داشته و از حدود 93.45 درصد در سال 1394 به 82.7 درصد در سال 1398 کاهش یافته است.
شرکت مجتمع جهان فولاد سیرجان، در راستای تحقق چشمانداز تولید 55 میلیون تن فولاد تا سال 1404، در تلاش است تا با تولید 2.7 میلیون تن آهن اسفنجی، 2.3 میلیون تن شمش فولاد و 2 میلیون تن محصولات نوردی و آلیاژی، به یکی از بزرگترین شرکتهای فولادی و تکمیلکننده زنجیره فولاد در منطقه گلگهر تبدیل شود. در نمودار 3، بخشهای اصلی تشکیلدهنده بهای تمامشده شمش فولادی شرکت مجتمع جهان فولاد سیرجان در سال 1398 نشان داده شده است. همانطور که دیده میشود، بیشترین سهم در بهای تمامشده شمش فولادی این شرکت را هزینه مواد اولیه با 57 درصد به خود اختصاص داده است. از آنجایی که تامین خوراک اولیه مسئلهای حائز اهمیت در توسعه صنعت فولاد است، این مجتمع در راستای تامین کسری خوراک کارخانه فولادسازی شماره 1 و 2 و نیز کاهش هزینههای تامین مواد اولیه خود، اجرای پروژه احیای مستقیم با ظرفیت تولید 1.7 میلیون تن را در دستور کار قرار داده است.
مسئله مهم دیگر در این زمینه، سهم بالای مواد نسوز و الکترودهای مصرفی این شرکت از بهای تمامشده آن است (حدود 26 درصد). اتخاذ سیاستهای مناسب در زمینه بهکارگیری تجهیزات و مواد باکیفیت و تامین داخلی این مواد میتواند زمینه مناسبی برای کاهش هزینههای خرید نسوزها و الکترودها و در نتیجه، کاهش بهای تمامشده محصولات فولادی فراهم کند.
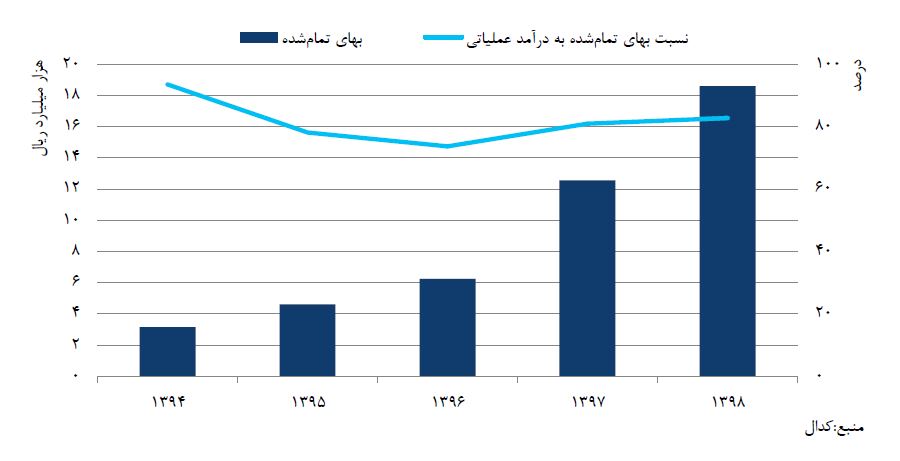
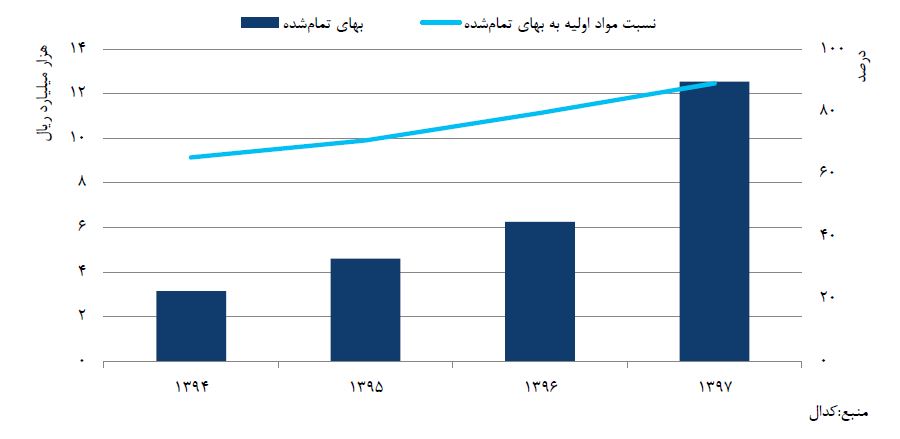
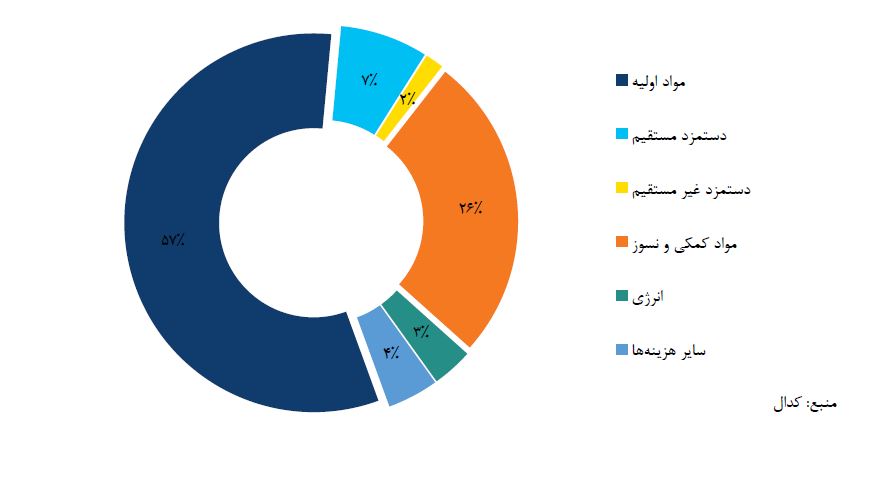
انتهای پیام/
ثبت دیدگاه