لازمه بهرهبرداری از ظرفیت حداکثری صنعت فولاد کشور در وهله اول توسعه اقتصادی داخلی و کشف بازارهای جدید صادراتی و تامینِ بهموقع مواد اولیه کارخانجات فولادی است. در این راستا، لازم است که مواد اولیه، اعم از سنگآهن و گندله، متناسب با نیاز در اختیار کارخانجات فولادی قرار گیرد تا آنها نیز بتوانند با حداکثر ظرفیت خود به تولید ادامه دهند و این مهم در کل زنجیره ارزش تا سطوح پایین ادامه داشته باشد. به همین دلیل، برنامهریزی و سرمایهگذاری مناسب به منظور اکتشاف معادن جدید و همچنین توسعه واحدهای فرآوری سنگآهن نقشی کلیدی در رشد بهرهبرداری از ظرفیتهای تولیدی صنعت فولاد ایفا میکند. همچنین در اولویت قرار گرفتن بومیسازی به منظور تامین مواد اولیه در شرایط تحریم و سرمایهگذاری در این حوزه، ثبات در سیاستگذاری، تامین منابع مالی، توجه به مکانیابی استقرار واحدهای فولادی و توجه به توازن ظرفیت زنجیره تولید از اصلیترین لازمههای بهرهبرداری حداکثری از ظرفیت تولید فولاد کشور به شمار میروند.
چالشهای پيشِروی صنعت فولاد
همانطور که گفته شد، یکی از مهمترین چالشهای بهرهبرداری از ظرفیتهای ایجادشده، دستیابی اقتصادی به بازارهای فروش و تامین مواد اولیه مورد نیاز است. در شرکت فولاد هرمزگان، گندله اصلیترین ماده اولیه است که در صورت عدم تامینِ بهموقع آن، واحدهای احیای مستقیم و فولادسازی این شرکت با مشکلاتی جدی مواجه خواهند شد. از آنجایی که تامین سنگآهن به دلایل مختلف جدیترین چالش پیشِروی سالهای آینده صنعت فولاد کشور برشمرده میشود و با توجه به اینکه اکثر ذخایر بزرگ سنگآهن در کشور شناسایی شدهاند و احتمال کشف ذخایر بزرگ و با صرفه اقتصادی بالا وجود ندارد و نیز تامین میزان کسری سنگآهن از منابع خارجی با چالشهای زیرساختی مواجه است، باید بهرهبرداری از معادن کوچک و متوسط داخلی در دستور کار قرار گیرد و فعالان در این حوزه تشویق به سرمایهگذاری و تبدیل همه تولیدات معادن کوچک و متوسط به کنسانتره و گندله شوند. در این بین، لازم است که این واحدها از حمایتهای دولت نیز برخوردار شوند.
گفتنی است که با توجه به اینکه بهرهبرداری 100 درصدی از ظرفیت صنعت فولاد و تحقق هدفگذاری برای افق 1404 بستگی به دستیابی به بازارهای صادراتی و موفقیت در صادرات این محصول به خارج از مرزهای ایران دارد، عدم امکان صادرات این میزان محصول به خارج از کشور و اشباع بازارهای داخلی منجر به کاهش ظرفیتهای تولیدی و در نتیجه، افزایش هزینههای تولید، کاهش ارزآوری به کشور، خواب سرمایه، بیکاری و از دست دادن بازارهای خارجی خواهد شد. در راستای جلوگیری از این مشکل، لازم است که بازارهای هدف جدید کشف شوند. نیاز زیرساختی کشورهای همسایه همچون عراق و سوریه به فولاد میتواند تا حدی این مشکل را کاهش دهد؛ همچنین لازم است با توسعه زیرساختها، هزینه حملونقل مواد اولیه و محصول کاهش داده شود. بومیسازی و جایگزینی قطعات تولید ملی و باکیفیت مورد استفاده در صنعت فولاد با نمونه مشابه خارجی میتواند هزینههای تمامشده تولید را کاهش دهد و امکان حضور در بازارهای جهانی را قوت بخشد. شرکت فولاد هرمزگان نیز در این راستا تولید کیفی محصولات و کاهش هزینههای تولید و توجه ویژه به بومیسازی و کشف بازارهای صادراتی جدید را در دستور کار خود قرار داده است.
نرخ بهرهبرداری در شرکت فولاد هرمزگان
بین افزایش ظرفیت تولید و هزینههای تمامشده رابطهای معکوس وجود دارد: هرچه میزان تولید افزایش یابد، هزینههای تولید کاهش خواهند یافت. در این راستا، در شرکت فولاد هرمزگان، بعد از تدوین نقشه استراتژی شرکت، اهداف واحدهای بهرهبرداری با رویکرد تولید ایمن با هدف کمترین هزینه تدوین شده و برای هریک از آنها شاخصهایی برای پایش و اندازهگیری مشخص شده است. با برگزاری جلسات منظم در کلیه سطوح به منظور اندازهگیری و پایش شاخصها، برای اجرای برنامههای مدون تلاش میشود. از جمله اقدامات مداوم در راستای افزایش نرخ تولید در واحد فولادسازی و ریختهگری میتوان به تحلیل انحرافات تولید از برنامه، تعریف و اجرایی شدن اقدام اصلاحی مناسب، راهاندازی و عملیاتی کردن مراکز هزینه و کنترل دقیق هزینههای اِعمالشده در هر مرکز هزینه به منظور کاهش هزینههای تمامشده تولید، کاهش توقفات اضطراری خطوط تولید، تامین باکیفیت و بهموقع مواد، ترویج کار گروهی و تعریف پروژههای بهبود، افزایش آمادهبهکاری تجهیزات، انجام تعمیرات پیشگیرانه منظم، کاهش زمان آمادهسازی ذوب، افزایش سرعت ماشین ریختهگری، الگوبرداری از شرکتهای موفق، کاهش ضایعات تولید و افزایش راندمان تولید اشاره کرد.
آهن اسفنجی: شرکت فولاد هرمزگان، در راستای افزایش نرخ بهرهبرداری در واحد احیای مستقیم، در سالهای اخیر فعالیتهای گستردهای داشته است. این شرکت توانست در سال 1397، با تولید بیش از یک میلیون و 691 هزار تن آهن اسفنجی، از ظرفیت اسمی تولید سالیانه خود عبور کند. همچنین در طی این سالها بهکرات از ظرفیت اسمی تولید روزانه و ماهیانه خود نیز عبور کرده است. از مهمترین فعالیتهای انجامشده در واحد احیای مستقیم میتوان به موارد زیر اشاره کرد:
- برگزاری جلسات مستمر با تامینکنندگان گندله، واحدهای خرید مواد اولیه و کنترل کیفیت در راستای تامین بهموقع و باکیفیت گندله؛
- انجام تعمیرات سالیانه (تعمیرات اساسی ریفرمر و تعویض تیوبها)؛
- انجام تعمیرات دورهای بهموقع؛
- تدوین و بازنگری دستورالعملهای تولیدی و تعمیراتی؛
- کاهش نرخ مصرف آب، گاز و برق؛
- کاهش توقفات اضطراری و تاخیر؛
- بهبود عملکرد غبارگیرها؛
- ارتقای عملکرد سیستم آب کولینگتاورها؛
- برنامهریزی برای شارژ گندله به کورههای احیای مستقیم در راستای کاهش هزینههای تولید؛
- شناسایی و مدیریت ریسکهای ایمنی اولویتدار و رفع مغایرتهای ایمنی شناساییشده؛
- بودجهبندی و کنترل هزینههای تولید؛
- تعریف پروژههای بهبود در راستای افزایش تولید.
همچنین شرکت فولاد هرمزگان، در راستای افزایش نرخ بهرهبرداری در واحد احیای مستقیم، طرحهای مختلفی از جمله پروژه نصب سولفورزدا، پروژه نصب کلدفلر و پروژه افزایش ظرفیت فناستک را در دستور کار خود دارد.
اسلب: شرکت فولاد هرمزگان در سال 1398 موفق به تولید بیش از یک میلیون و 460 هزار تن اسلب شد که نسبت به سال گذشته 1.3 درصد رشد تولید داشته و 97.33 درصد از ظرفیت اسمی خود را محقق کرده است. در سال جاری نیز، با توجه به تحریمهای پیشِرو و در راستای حفظ سهم بازارهای داخلی و صادراتی، این شرکت افزایش کیفیت محصول را در دستور کار خود قرار داده و با تدوین برنامه یک میلیون و 520 هزار تنی در واحد فولادسازی، از ظرفیت اسمی خود عبور خواهد کرد. شرکت فولاد هرمزگان، با تدوین هدف «افزایش کمیت و کیفیت و تحویل بهموقع محصولات» در نقشه استراتژی شرکت و با رویکرد کاهش هزينههای تولید، افزايش بهرهوري و راندمان توليد و با کار تيمي منسجم و برنامهریزیشده، در پی محقق کردن اهداف خود است. مهمترین فعالیتهایی که در راستای افزایش نرخ بهرهبرداری از ظرفیت تولید اسلب انجام شده به شرح زیر است:
- کاهش توقفات اضطراری و تاخیر واحدهای فولادسازی و ریختهگری مداوم؛
- 2.افزایش میانگین نرخ شارژ فلزی به کورههای قوس؛
- افزایش سرعت ماشین ریختهگری؛
- افزایش بازده کورههای قوسی و ریختهگری؛
- بهبود کیفیت سرباره کوره قوس الکتریکی؛
- افزایش ظرفیت پاتیلها؛
- کنترل مستمر فرایند تولید؛
- تدوین و بازنگری دستورالعملهای تولیدی و تعمیراتی؛
- انجام تعمیرات سالیانه و دورهای بهموقع؛
- کاهش مصارف نسوز و الکترود؛
- ارتباط مستمر با واحدهای احیای مستقیم و آهکسازی در راستای افزایش کیفیت آهن اسفنجی و آهک ارسالی؛
- ارتباط موثر با واحد خرید مواد اولیه و قطعات یدکی در راستای افزایش کیفیت مواد و قطعات یدکی؛
- بهبود کیفیت داخلی و سطحی اسلبهای تولیدی؛
- کاهش نسبت تولید محصولات خارج از سفارش مشتریان.
همچنین شرکت فولاد هرمزگان، در راستای افزایش نرخ بهرهبرداری در واحد فولادسازی و ریختهگری مداوم، پروژههایی را در دست اقدام دارد.
بریکتسازی: واحد بریکتسازی شرکت فولاد هرمزگان شامل دو دستگاه ماشین بریکتسازی با ظرفیت تولید چهل تن در ساعت است که وظیفه تبدیل نرمههای آهن اسفنجی به بریکت را بر عهده دارد. با توجه به ظرفیت خالی ماشین بریکتسازی، در سالهای اخیر تبدیل نرمههای مازاد شرکتهای مجاور به بریکت و فروش آن نیز در دستور کار قرار گرفته است. شرکت فولاد هرمزگان، در راستای افزایش نرخ بهرهبرداری و استفاده حداکثری از ظرفیت خالی ماشین بریکتسازی، برنامههای مختلفی از جمله برنامهریزی در راستای افزایش نرخ مصرف بریکت در واحد فولادسازی، تعمیرات اساسی ماشین شماره 2 شامل تعویض سگمنت و تجهیزات برقی و ابزار دقیق، نصب شوت بر روی نوار ورودی و شارژ جداگانه نرمه در راستای جلوگیری از کمبود نرمه آهن اسفنجی، تعمیرات اساسی استاکر بریکتسازی و برگزاری جلسات مداوم با واحد خرید مواد اولیه در راستای تامین باکیفیت ملاس و آهک هیدراته را در دستور کار خود قرار داده است.
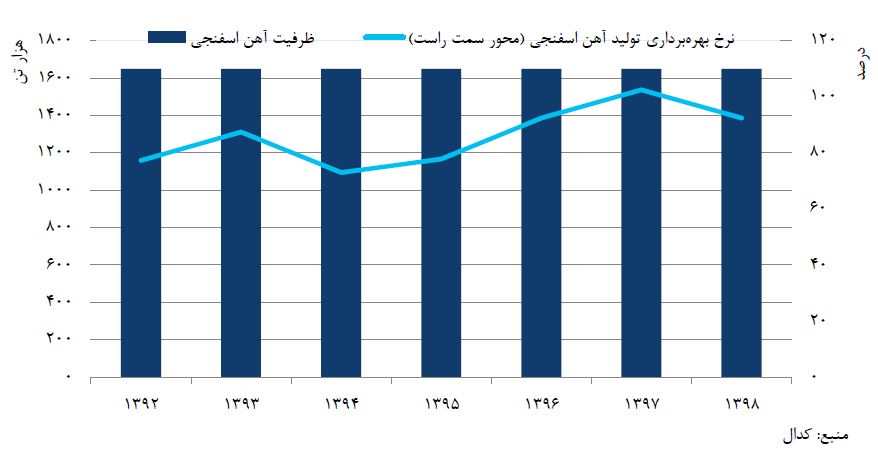
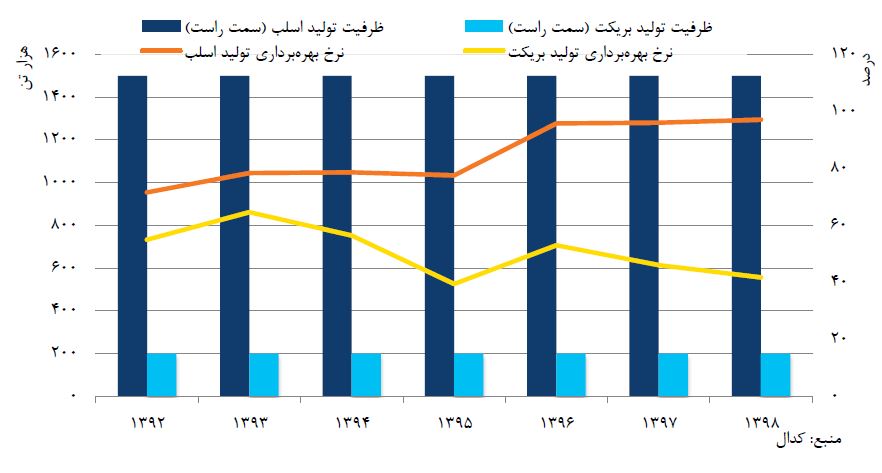
انتهای پیام/
ثبت دیدگاه